Tasks
At the time, most of tasks at the Tile Works
were performed manually. From digging
the clay, to loading the fired tiles, the work was hot, dirty and physically
demanding. Although no records still
exist, it is reasonable to assume that the workers at the tile works may have
been paid at fairly low rates. A
leading hand made sure that work continued.
Pitmen were either covered in dust or mud, depending on the weather.
Pitmen
The process began with the Pitmen who dug the
clay from the pit. This was done with
pick and shovel into a steel truck. The
truck was then wheeled on a steel rail track to a collection point or tipped
into a cart. Work in the pit was
captive to the vagaries of climate. If
the weather was too wet, no work was done and the men did not get paid. At the
time, horses pulled carts of clay to an elevator in the pit that took the clay
to the top. Clay was transported the
short distance to the works where it was stored under cover until needed for
processing.
Clay or shale was originally
removed and broken up from the face by using a “spalling hammer.”
Spallers had a high incidence of eye-injury as eye protection in earlier times
was not mandatory. Small trolleys of up to one ton were filled by hand
and pushed along narrow-gauge rails to either a “truck hole” where the contents
were tipped into a skip that was then hauled up an inclined cable railway to
the brick works. The bottom of the pit may have had a network of
rails.
Other names for pitmen were
Quarrymen, Shooters, Jumpermen or Breakers. They also dug drains and sump-holes to
keep the quarry face clear. The Clay
Getter-gets clay and a General Hand did anything else. Pitmen worked by removing clay from a
series of descending horizontal terraces, by digging, filling and wheeling away
the clay. Quarrying soft clay
doesn’t need explosives but was done either by hand or mechanical excavator
with continuous buckets.
Clay
was stored and left to partially dry before being crushed and fed into a
Pugmill. This was a large wooden vat
with a central shaft with paddles attached.
A horse was hitched to a large horizontal pole attached to the
shaft. The horse spent its days walking
around and around, mixing the clay and water (pug).
This Pugmill was used at the Ordish Brickworks in
Dandenong and is similar to those used at other works. Some works had their crushers located
in the clay pit where the crushed clay was then transported by a conveyor
direct to the works. This had the benefit of separating a very dusty part
of the process, and allowing wind to disperse the dust within the pit.
For the purpose of storing and protecting mined
clay, a large drying shed would have been built. This shed would have been a large open sided area with a
corrugated iron roof. The open sides
allowed for airflow and the sides could be enclosed if the weather was
inclement. Clay was stored before going
into a hopper at one end of the process and “green” (unfired) bricks were
stored there for drying for up to a week before being loaded into the kiln.
Drying Shed at Eureka Tiles
A hopper fed the clay into a press and the
green tiles were wheeled to the drying shed.
The wheelers then took the “dry” tiles to the kiln. Wheelers were the people who pushed
wooden barrows of tiles to the Setters or from the Draggers. Generally,
the rule of thumb was that the load should not exceed 50kg. The centre of
gravity of the load was the determinant. Usually it did not go above the
height of the wheelbarrow handle when the wheeler was standing upright.
Setters
A setter does all the work inside
the kilns. Green tiles are
soft and require careful handling during this process. Work is restricted only
by the capacity of the tile making machines. In some works, tiles arrived at the
kiln in the form they were placed inside, so the setter just ran them in using
an overhead carrier. This
was usually done in a Clamp, (or Scove Kiln) not other types of kiln.
Tiles
were set in rows or “bolts.” A good setter would arrange the ends of the
tiles in the bolts so you could see from the front end of the stack, to the
back. This lets the air flow uninterrupted so the steam in the drying
stage and the gasses in the firing stage can pass without staining the
tiles. Tiles are set as close to the roof as possible in an arched kiln
to reduce the effects of hot air rising. As the stack rises, the space
between the tiles is reduced. Setters must keep the rows in line with the
flues to ensure proper airflow. Sometime a Setter will also build flues
into the stacks to aid airflow. Supervision of Setters was
essential to ensure the correct positioning of tiles in the kiln. Even
firing results in even tiles. When the kiln is opened, the fired tiles
were then sorted, as they were unloaded.
Unloaders
Burners
The most important and specialized job at the works was
that of a Burner. They were responsible
for controlling the temperature of the fire.
This job was to ensure that opening and closing the flues allowing heat
into the chamber controlled the drying process and shrinkage.
Controlling the evaporation of moisture from and
around the tiles was the first stage of a Burners duties. As around 20% of the raw tile was water,
evaporation was essential. Initially,
the heat of the kiln heated the water in the tile, causing it to expand and
turn to steam. This is the “baking”
stage. Burning is complete when the
fired tile does not shrink any more and has a distinct ring when hit with a
metal object. This is where the
burner’s skill comes in because if the tiles are fired too long, they begin to
distort. There is not much of a
difference between a fired tile and a “blown” tile. A Burner would judge the firing by the colour of the fire inside
the kiln. Depending on wind direction,
smoke would settle over the surrounding area.
This created problems when washing was drying on clothes-lines.
Unloading a kiln was another
specialized job. In larger companies,
the job of loading and unloading was split between the Setters who loaded the
tile into the kiln and the Draggers who unloaded them. This was not a popular job. Sometimes the Draggers would have their
trousers catch fire because of the heat from the tiles. To combat the
effects of heat, Draggers would wear leather or rubber “mits” or
“cots.” They consumed copious quantities of water, along with salt
tablets. Beer was generally an after hours essential. It was hot, dirty work. Draggers would
load tiles onto a trolley, usually made of wood, with a rubber wheel.
The
different types of clay around Ballarat produced bricks and tiles of varying
colour and quality. These tiles were
produced initially in a “Scotch Kiln.” In
the English-speaking world, this is the term for a kiln used to make a smaller
supply of bricks. It is also known as a
Dutch or Scove Kiln. It is the type of
kiln most commonly used in the low volume manufacture of tiles.
It is a roughly rectangular
building, open at the top, and having wide doorways at the ends. The sidewalls
are built of old or poorly made tiles set in clay. There are several openings called fire-holes, or "
eyes," made of firebricks and fire clay, opposite one another.
The naturally occurring minerals that are kiln fired to
burn in their colour and strength determined the colour of clay bricks and tiles.
The composition of the raw materials as well as the firing process would cause
each batch to differ. The resultant colour variation was inherent in the
process and part of the visual appeal of the tiles. Usually those tiles
contained approximate amounts of the following ingredients:
Silica (sand) between 50% to 60% by weight
Alumina (clay) between 20% to 30% by weight
Lime between 2 to 5% by weight
Iron oxide up to 7% by weight
Magnesia – less than 1% by weight
Colour is not only determined by the colour of the clay and
its chemical composition, but also:
The colour of the sand used in the moulding;
The moisture content before firing;
The fuel used to fire the kiln;
The volume of air during firing; and
The temperature in the kiln during firing.
Tiles
What is a terra cotta tile? Put simply, they are man-made rocks.
We take sedimentary material and turn it into a metamorphic one by applying
heat. They are small individually moulded rectangular blocks of clay of
uniform size that are baked in a kiln until hard and used as a building or
paving material. The first attempt to standardize the size of a brick in
England was in 1477. Much later, Queen Elizabeth 1st granted a
charter to brick and tile makers, after which a standard size of 9” x 41/4” x 2
¼ inches became common, although variations in size continued. In 1849
the Statute Brick was required to be this size. Today, they are produced
in a standard size; 2 ¼ inches by 3 ¾ inches by 9 inches, or 75mm by 115mm by
230mm. Whatever size, the ratio of 4:2:1 is standard. Clay bricks and tiles come in several basic types;
The clay for stiff plastic tiles has slightly higher water content
(up to 17%). The clay is forced under pressure from an auger into a
mould. A different machine is
needed to make wire-cut tiles. The water content is higher
again (up to 25%). The clay is forced using an auger into a conical tube
tapering to a die. The resulting rectangular sausage of clay is then cut
into tiles by a wire or wires. Extruded tiles
are usually smooth but can also have a pattern or texture applied.
As an example, these are the Scotch Kilns at Wonthaggi with the
brick making plant behind. Note the
timber for fuel stacked around the kiln.
After the dried tiles are loaded into the kiln, the ends
or wickets are built up, and plastered over (or scoved) with clay. At first the
fires are kept low, simply to drive off the moisture. After about three days the steam ceases to rise and the fires are
allowed to burn up briskly. The draught
is regulated by partially stopping the fire-holes with clay, and by covering
the top of the kiln with old bricks, boards, or earth, so as to keep in the
heat.
It takes between 48 to 60 hours for the tiles to be
sufficiently fired, and they will have shrunk to the appropriate size. The fire-holes are then completely sealed
with clay (scoved) and all air excluded.
The kiln is then allowed to cool gradually.
De-aired tiles made by vacuum extrusion were still in the
future and local bricks were fired in a variety of wood and coal fired periodic
kilns. The ability to control
temperatures was still more art than science.
High temperatures in the kiln produced high-strength bricks. Areas in the kiln with lower temperatures
produced lower quality bricks. This
resulted in a variety of colour and absorption rates.
Fuel
Size Of Kiln
Time Of Burning And Production
Tunnel Kiln
About a half-ton
of soft coal is required for burning 1000 tiles. The exact quantity depends
upon the type of clay, quality of fuel, and the skill in setting the kiln. Most Scotch Kilns were fired with wood. This wood was cut into lengths of around 1
metre. Some Scotch Kilns were fired
with half wood, half coal. Some with
just coal, others, just wood, depending on the quality of the coal.
A convenient size for a Scotch kiln is about
60 feet by 11 feet internal dimensions, and 12 feet high. This will contain
about 80,000 bricks. The fire-holes are 3 feet apart. These kilns are often
made 12 feet wide, but 11 feet is enough to burn through properly. The existing pictures of the Wonthaggi kiln
show a much smaller kiln (or kilns) of around 20 to 30,000 bricks per
firing. This is likely to have been the
size of the original kiln at Eureka.
A kiln takes on an average a week to burn,
and, including the time required for crowding and emptying, it may be burnt
about once every three weeks, or ten times in an average season. This will produce about 400 to 600,000
bricks or tiles which is about as many as would be turned out by two hand
moulders in full work. The tiles in the
centre of the kiln are generally well burnt.
Those at the bottom are likely to be very hard, some clinkered.
Those at the top are often badly burnt,
soft, and unfit for exterior work. It took one week to stack and arrange the bricks or tiles in the
kiln. It took another week to fire them, consisting of three days to dry
out the bricks or tiles and four days at 2000 degrees Celsius. It took
another week to unpack. These kilns
usually had metal bracing to prevent them from falling apart during
firing. This sometimes consisted of pieces of old steel railway track
buried vertically about one and a half meters into the ground at regular
intervals around the kilns. These posts went to roof height and metal
strapping or bars were fixed horizontally around the kiln to brace the
brickwork.
At the time, these kilns were
rare in Australia but were quite common in the United States, with over 600
being used. This was what was in use
later at Eureka Terra Cotta and Tile Company.
The Commonwealth Brick works in Canberra had two, and one was used in
Hobart. Selkirks in Ballarat had also
built a tunnel kiln in the early 1960s.
A tunnel kiln is a type known as a continuous flow kiln. Tunnel Kilns were a later addition that
consisted of a long straight “tunnel” through which the tiles pass on trolleys
through the various stages of cooking.
The initial drying stage is first, then warming, firing, and cooling.
A tunnel kiln, as the name implies, is a tunnel
of firebricks approximately 4’6” wide, with a 6’ high arched roof. The firebricks are about 12’ Square and
about 6” thick. The tunnel itself can
be up to 300’ long. The Ballarat kiln
was not that long. The floor of the
kiln was fitted with rails along which a series of kiln cars progress. Sand filled troughs were fitted along the
sides of the rails and the space between the rails was used as a cooling and
inspection chamber. Furnace oil was
used as a fuel.
Cross Section of a Tunnel Kiln
At the entrance to the kiln, a double lock gate
was installed to permit the entrance to be air-tight. An hydraulic ram pushed the last kiln car into the tunnel. Because all the cars were connected, this
meant that the first car with the fired tiles was pushed out the other
end. The kiln cars were made of metal
and had four wheels. They had metal
strips to the side to fit with the side troughs to form a heat seal. The kiln cars carried firebrick on the
bottom to also form a heat seal and provide insulation between the kiln and
rails and the metal undercarriage of the cars.
The top of the kiln cars were also covered with refractory material.
There were openings in the roof and sides of
the firing zone. This was a
forced-draught system that allowed hot gasses to be directed to the pre-heating
and drying zones. It also removed waste
gas from the feeding section. Rails,
trucks and transfer platforms were there to allow transfer from the tile making
plant, the unloading section and back to the tile making plant.
Tiles were fed on a conveyor belt from the tile
making section onto the kiln cars. The
setting station could raise the kiln cars to simplify the setting of tiles on
the cars. Loaded cars were either
loaded into the kiln, or set aside for firing as time permitted, either at
night or during quiet times.
At intervals of about one hour, a car was
pushed into the air lock chamber of the kiln.
After the outer door was closed, the green (unfired) tiles were pushed
by the hydraulic pusher into the first zone. This served as a drying zone and was fed with waste gasses. The tiles were heated to higher temperatures
as they progressed through the kiln.
They went through a pre-heating zone before going into the firing zone
for a relatively short time. After being
fire, the tiles went through a cooling zone where they cooled sufficiently to
be handled.
After firing, the tiles moved to the unloading
zone where they were unloaded and stored awaiting loading onto trucks for
delivery. Sometimes they were loaded
directly onto trucks. The kiln cars
were then ready for re-use.
There were many advantages of a tunnel kiln
·
The
amount of staff needed was about 30% less than traditional brick making; for
example, a kiln attendant could operate the oil firing as well as operating the
kiln cars;
·
Fuel
costs were significantly lower, being 1/3 less than coal fired kilns; oil was more expensive, but produced a more
uniform heat with less rejects. Oil was
fed automatically and did not need a firer like those at a Hoffman kiln. Thermal efficiency was much better than
coal. (In the day, this was 18,500 BTUs
for oil and 13,500 to 14,500 BTUs for black coal.)
·
Heat
was constant and did not fluctuate like other continuous kilns.
·
Maintenance
and upkeep costs were lower because there was not the constant expansion and
contraction experienced in Hoffman kilns.
·
Heat
control means better firing and product uniformity.
The Firing Area of a Tunnel Kiln Installed at the Colac Brickworks
Bricks being loaded into a Tunnel
Kiln at the Colac Brick Works in the 1950s.
Note the metal skirt under the kiln car, the brick insulation under and
over the bricks. The outer gate is
visible at the top of the picture.
Brick, Tile and Pottery Workers
There are many different tasks
undertaken at a brick or tile works. These depend on the type of work and
the type of kiln. Modern automated works have caused the loss of many of
these occupations, having only quarrymen at the beginning of the process and
unloaders at the other. Until the 1970s, there were different employment
categories for men, women and juniors. Female rates were about 1/3 less
than the rate for males and the junior rate was about 1/3 of the adult
rate. The following is a list of categories from the Department of Labour
and Industry Pottery Board in September 1968.
These many skills were developed
and employed at a brick, tile or pipe works.
As plant became larger and more sophisticated, so too was the division
of labour. Because most works are now almost fully automated. These skills are no longer performed. Sometimes when special orders for hand made
bricks at one of the few surviving smaller specialist works comes in, some of
the skills are still used.
Leading Hand
A leading hand that was a person
who assumes any responsibility other than that customarily done by an ordinary
employee usually controlled the manual work in the works. They were usually men of long
experience in most, if not all facets of brick making who would assume the
responsibility of training all the other workers in their tasks. An additional wage loading was paid to
a Leading Hand.
Pitwork
Quarrymen, Shooters or Jumpermen
worked in the pit and were also known as pitmen or breakers. They also dug drains and sump-holes to
keep the quarry face clear. The Clay
Getter-gets clay and a General Hand do anything else. Pitmen worked by removing clay from a
series of descending horizontal terraces, by digging, filling and wheeling away
the clay. Quarrying soft
clay doesn’t need explosives but was done either by hand or mechanical
excavator with continuous buckets. Later
dragline excavators or power shovels were used. This does not leave loose material on
the face as it leaves a smooth surface.
Setters
A Setter or Stacker does all the
work inside the kilns. Green
bricks and tiles are soft and require careful handling during this process.
Work is restricted only by the capacity of the
machines. Up to 3
setters could work in a kiln. Bricks
or tiles were brought to the door of the kiln and the setters would place them
inside. In some works,
bricks or tiles arrived at the kiln in the form they were placed inside, so the
setter just ran them in using an overhead carrier. This was usually done in a Clamp, not
other types of kiln. A good
Setter could place up to 70,000 bricks per day.
For this rate to be achieved, a
conveyor delivered the bricks or tiles to the Setter and could be adjusted to
the height of the stack as it became progressively higher.
Bricks or tiles are set in rows
or “bolts.” A good setter would arrange the ends of the bricks in the
bolts so you could see from the front end of the stack, to the back. This
lets the air flow uninterrupted so the steam in the drying stage and the gasses
in the firing stage can pass without staining the bricks. Bricks or tiles
are set as close to the roof as possible in an arched kiln to reduce the
effects of hot air rising. As the stack rises, the space between the
bricks is reduced.
Setters must keep the rows in
line with the flues to ensure proper airflow. Sometime a Setter will also
build flues into the stacks to aid airflow. Setters placed the
bricks or tiles in rows called “blades.” Each blade was made up of 1000 bricks or
tiles, 50 long and 20 high. Usually, to
make a stack, two blades were made together and supported at heights of 5, 10
and 15 bricks high. Supervision of
Setters was essential to ensure the correct positioning of bricks or tiles in the kiln. Even firing results in even
bricks or tiles. When the kiln is opened, the fired bricks and tiles were
then sorted, as they were unloaded, usually into “firsts”, “seconds” and
“clinkers.” Salary was dependent
on the type of kiln.
Draggers
Unloading a kiln was another
specialized job. In larger companies,
the job of loading and unloading was split between the Setters who loaded the
bricks or tiles into the kiln and the Draggers who unloaded them. This was not a popular job. Sometimes the Draggers would have their
trousers catch fire because of the heat from the bricks. This sometimes
happened on Fridays when the fire would catch up with the bricks or tiles
. To combat the effects of heat, Draggers would wear leather or rubber
“mits” or “cots.” Draggers consumed copious quantities of water,
along with salt tablets. It was hot, dirty work. Draggers would
load bricks or tiles onto a trolley, usually made of wood.
Wheelers
Wheelers were the people who
pushed the wooden barrows of bricks or tiles to the Setters or from the
Draggers. Generally, the rule of thumb was that the load should not
exceed 50kg. The centre of gravity of the load was the determinant.
Usually it did not go above the height of the wheelbarrow handle when the
wheeler was standing upright.
Automatic Extruder Operator (i.e.
a man operating extrusion, dressing and loading machinery)
Automatic Machine Loader and
Unloader Assistant
Bitumen Jointer
Burner
Clayhole Men (Employer to provide
tools)
Drawer (i.e. drawing inside kiln)
Drawer, other
Drying Room Attendant
Feeder of Pipe Machine
Greenware Sorter
Grinding Attendant
Hand Feeder of Raw or Burnt Clay
into crusher or grinding pan
Junction Sticker and/or Knocker
Operator
Junction Repairer of Burnt Ware
Kiln Labourer (i.e. a person
whose duties comprise assisting a Placer, Drawer Setter or Tunnel Kiln Operator
and/or the cleaning of fire holes and/or flues)
Machine Rigger
Mandril Operator
Man carrying or wheeling into or
out of kiln or to or away from kiln
Man in charge of Pug or Mixer
Machine
Man operating or taking off
machine making Siphons, D traps, inlets and the like
Man taking off Pipe Machine
Man sorting pipes
Man working Pipe Flanging Machine
Man boring or using explosives
Mouldmaker
Packer of goods into Railway
Trucks
Pipe or bend dresser
Pipe Cutter of burnt ware
Presser
Setter (i.e. setting inside kiln)
Setter, other
Tunnel Kiln Operator
Hand Dipper and/or Spray
Operator
Kiln Placer and/or Unloader
Man Hand Pressing dust tiles or
working semi-automatic tile press
Slip House Attendant
Tunnel Kiln Operator
Automatic Glazing Machine
Attendant, including Feeder and/or Cranker
Boxer, including Tile Sorters
Hand Dipper and/or Spray Operator
Burnt Ware Sorter
Caster
Clay Shaper
Driller and/or Grinder of unburn
ware
Glazer
Greenware Sorter
Grinder of burnt ware required
using calipers
Grinder of burnt ware other, 1st six months experience
Jolly Hand and/or Profiler
(including semi-automatic machines) 1st six months experience
Jug Cutter
Kiln Car Placer and/or other
Unloader
Male Machine Operator
Man cementing and/or leading
insulators
Man sanding insulators
Mill Room Hand
Mould Maker
Packer
Presser (screw and lever type
inclusive)
Presser (automatic)
Pug Mill Hand
Sagger Maker
Sagger Maker’s Assistant
Setter inside kiln
Thrower-1st six months experience
Thereafter
Tunnel Kiln Operator
Turner (required to use calipers)
1st six months
experience
Thereafter
Turner other 1st six months experience
Thereafter
Assemblers
Bitumen Sprayer
Cleaners and Finishers
Glazer
Glazer’s Attendant
Glazing Machine Attendant
(Automatic)
Jug Trimmer
Packer of Fired Ware
Machine Operator
Placer
Presser (screw or lever type)
Press Operator (Automatic)
Spray Operator
Test Room Hand
Turner (required to use calipers)
1st six months
experience
Thereafter
Turner, other 1st six months experience
Thereafter
Dipper and/or Spray Operator
Jigger Hand (including
semi-automatic machine)
Jolly Hand (including
semi-automatic machine)
Mouldmaker
Placer and/or Drawer
Polisher of Glazed Ware
Slip House Attendant
Tunnel Kiln Operator
Cup and Caster Sponger
Dipper
Fixing handles and/or spouts
Gilder on glaze, Gilder, Bander,
Stamper
Handle Maker
Handle Trimmer and/or Cutter
Jigger Hand (including
semi-automatic machine)
Jolly Hand (including
semi-automatic machine)
Packer/ Carton Packer
Polisher of glazed ware
Tower
Transferer-slide on
Caster-Sanitary Ware
Caster-other
Dipper and/or Spray Operator
Grader of Glazed Ware
Green Ware Inspector
Grinder of Burnt Ware
Hand Feeder of raw or burnt clay
into crusher or grinding pan
Kiln Car Placer and/or Unloader
and/or other Placer
Man fixing handles or spouts
Mouldmaker (blocks and
cases)
Mouldmaker (other)
Packer
Slip House Attendant
Tunnel Kiln Operator
Turner, Jolly Hand and Jigger
Hand (including semi automatic machine)
Caster-Sanitary Ware
Caster-other
Dipper and/or Spray Operator
Fixer of Handles or Spouts
Jug Trimmer
Packer
Turner, Jolly Hand and Jigger
Hand (including semi automatic machine)
Caster-(other)
Dipper and/or Spray Operator
Mouldmaker
Packer
Placer and/or Unloader
Slip House Attendant
Dipper and/or Spray Operator
Examiner and/or Finisher of Green
Ware
Packer
Placer and/or Drawer
One of the most productive areas
often overlooked when reporting on brick or tile making is the use of
explosives to loosen the clay or shale. In
the end, it was explosives that caused the closure of a number of quarries
close to populated areas. Councils,
including Ballarat passed by-laws prohibiting the use of explosives.
Using explosives for blasting is
sometimes necessary for the recovery of clay or shale in many quarries.
Blasting can cause noise and vibration that have an impact on the surrounding
environment. Proper security of explosives and control of blasting practices is
necessary to ensure the safety of employees and the protection of the community
and environment from adverse effects.
Blasting will result in both
ground and airborne vibration. The latter commonly includes both audible noise
and vibration known as air blast, that causes objects to rattle and make noise.
At the levels experienced from blasting associated with quarrying, structural
damage to adjoining properties is unlikely to occur. In addition, the noise
levels experienced from blasting at a quarry site, are unlikely to cause any
hearing damage to anyone outside the worksite.
Duties include;
check blasting areas to make sure
that safety regulations are met
cut channels under working faces
check borehole depths and ensure
that they are clean
decide quantity of explosives
required
insert detonators and charges
into holes
connect and test or inspect the
blasting circuit
fire charges
inspect the area to make sure all
explosives have been detonated
check site safety after blasting
(falling rock hazards, underground mine roof supports and harmful fumes, for
example), and declare the area safe
Annoyance and discomfort from
blasting can occur when noise startles individuals or when air blast or ground vibration
causes vibration of windows or other items at a sensitive Site. The degree of
annoyance will therefore be influenced by the level of air blast and vibration
as well as factors such as the time of day, the frequency of occurrence and the
sensitivity of individuals.
In most cases, a competent
operator can reasonably predict the level of air blast and ground
vibration. However the generation and transmission of air blast and
ground vibration is affected by a number of factors including blast design,
meteorology (particularly wind speed and direction and temperature inversions),
topography, geology and soil water content. It is possible that on some
occasions the level of air blast and/or ground vibration will exceed the
predicted levels. These days, several
people are involved when once, only a Shot Firer was used. Shot firers
assemble, position and detonate explosives to break or dislodge rock and soil
or to demolish structures.
Security of explosives was viewed
somewhat flexibly in former days. Some were stored in sheds secured with
a bolt and padlock. Sometimes, the explosives were stored in a dugout in
the quarry with a loose fitting door. There were several thefts of
explosives and detonators from often poorly secured stores.
Creswick
Powder Magazine
Hand operated jumper bars were
used in most pits until the introduction of electric rotary rock drills.
Explosives are now electrically fired, making the process safer. This is
now the only method used in pits today. The use of a “cuddy” or safety
shield is also mandatory. The dangerous practice of “bulling”, or
dropping explosives with the fuse lit into a hole by hand or using a tamping
rod has now thankfully passed into history.
Following an explosion, “barring
down”, or manually clearing loose clay or shale from the face was done.
An early safety device was to tie a rope around the waist of the worker in case
of a collapse on the face. Even hard-hats were not worn. Later,
safety belts and hard hats were made mandatory. Softer clay was
loosened by hand or mechanically. Shale was then removed using a power
shovel or excavator.
This image shows a quarry worker
gently pushing an explosive charge down a hole bored in the rock. The reel next
to his right foot contains a cable to permit detonation from a safe distance.
The work is hot, dirty and dangerous. As well as the obvious trauma
hazard, this procedure (shot-blasting) can generate large concentrations of
silica dust.
Silicosis is a serious and
progressive disease. The term mixed dust fibrosis describes the pulmonary
disorder caused by the inhalation of silica dust simultaneously with another
non-fibrogenic dust. Most dust particles in a brick works settled quickly
as they were large and were stopped by the nasal passages. Finer
particles of less than.0002” were dangerous, but Government testing found no
particles that exceeded the minimum standard. To reduce dust inside the
works, grinding was done outside where the wind dispersed the dust. Good
in summer but quite cold in winter.
Clay or shale was originally
removed and broken up from the face by using a “spalling hammer.”
Spallers had a high incidence of eye-injury as eye protection in earlier times
was not mandatory. Small trolleys of up to one ton were filled by hand
and pushed along narrow-gauge rails to either a “truck hole” where the contents
were tipped into a skip that was then hauled up an inclined cable railway to
the brick works. The bottom of the pit may have had a network of
rails. Later, bulldozers were used to push the clay to the
conveyor. This is many times more efficient than by hand.
Some brick and tile works had
their crushers located in the clay pit where the crushed clay was then
transported by a conveyor direct to the works. This had the benefit of
separating a very dusty part of the process, and allowing wind to disperse the
dust within the pit.
Clay came originally quarried from the pit nearby and
brought to the works by conveyor. It was milled while still moist and
went through a pug mill where it emerged as a continuous mass onto a roller
table where it was cut into blocks. These blocks were transported into a
double-sided press where they were shaped into tiles. Excess water was
expelled during pressing. At the Eureka Tile Works, the green tiles moved
from the press onto a conveyor belt where they were trimmed by hand of any
surplus clay.
Tiles were then put onto trays and moved to the drying racks where they
dried for up to two weeks. They then moved to the drying floor where they
were placed on racks to dry. After drying, they were packed onto a barrow
that was placed onto a lift and lowered to where they were loaded into the
kiln. The dried tiles were fired in stages at up to
1100C. After cooling, the fired tiles were removed, graded and
stored ready for shipping. Drying was done upstairs where the heat from
the kiln was ducted to aid the process. They dried for up to two
weeks.
Evans Brothers Tile Works, Oakleigh, Late 1940s
Tile Cleaning, Evans Brothers Oakleigh 1947
As seen here, bricks and tiles had there rough edges
trimmed. Here, workers use their hands. but often a wire called a “bow”
was used on the soft clay in the moulds.
The following information was
given to me by Pauline Holloway who had obtained it from Max Phillips. Max has done an excellent job compiling
it. I have modified it somewhat to make
it more current. As discussed
previously, the Architectural firm of Messrs George W Clegg and William Miller
of 5 Lydiard St, established in 1905, was enjoying a very extensive practice
throughout Ballarat and country districts and was engaged in importing French
terra cotta tiles and English slates for roof construction.
William Miller approached a potter, August E (Otto)
Steinkraus, who owned and operated a pottery on the site adjacent to the Eureka
Stockade Reserve where the former Eureka Tiles Pty Ltd office and factory still
stand, to enquire about a special chimney pot and asked the potter why he did
not make roofing tiles. The potter replied he had excellent clays for the purpose
but was too old to be launching out into an extensive industry. Otto Steinkraus would have been 62 years of
age at the time.
After some investigations Messrs
Clegg and Miller purchased the pottery and started the first roof tile
manufacturing factory in the State. The business started off in a small way in
a building about 100 ft long by 30 ft wide with one small kiln, and according
to an article in the edition of the Ballarat Courier on the 27th of
October 1911, they engaged the potter Steinkraus as manager. The article
read:- "An industry which is
likely to give a large amount of employment in the near future has been
thoroughly established in Ballarat East.
We refer to the Eureka pottery, established under the management of Mr.
A E Steinkraus. Machinery has been
installed for all kinds of pottery ware; but the chief product will be roofing
tiles and fancy terra cotta ware. An
interesting exhibit of terra cotta ware is now on show at Gordon Bros".
An early photograph
of the works from around 1930
The
first batches of tiles were made with the machinery imported from England only
to discover that the clay was not entirely suitable which necessitated research
for a suitable deposit of clay. From investigations, it was discovered that the
clay deposits from certain abandoned sluicing and dredging claims proved on
analysis to contain pure terra cotta clays. These were possibly more valuable
than the gold extracted from them previously, being in readily workable form.
Immediate steps were taken to secure the clay to last the Company in excess of
fifty years, and at the inaugural meeting held on the 12 th of April 1913, the
proprietary company “Eureka Terra Cotta and Tile Co Pty Ltd, came into being
with a working capital of 10,000 pounds. This amount was expended during the
next 12 months building workshops to cover an area of over half an-acre, with
two modern kilns and machinery to produce 5000 tiles per day.
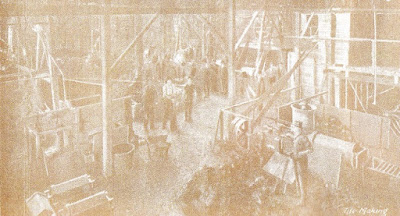
Early success in firing roof
tiles prompted further expansion and it was decided to float the venture into a
public company. Even at this early stage, over 100 separate items were being
fired by the company, including chimney pots, fancy ridging and hips; besides
many attractive gable finials. Capital
of 100,000 pounds in shares of one pound each was sought in a prospectus drawn
up by the promoters. Provisional directors of the new company were :-
Frederick Sutton, Esq; (Suttons
Pty Ltd., of Melbourne, Ballarat, Bendigo and
Geelong), chairman.
Frank Hermarn Esq. (Goller and Co
Pty Ltd., Ballarat);
John Robertson Wotherspoorq Esq.
(Wotherspoon and Co., Merchants, Beaufort);
George William Clegg, Esq. (Clegg
and Miller, Architects, Ballarat);
Hugh Victor McKay (Manufacturer, Sunshine) who was to join
the board after the company' s incorporation.
The first secretary and one of the driving forces behind the
establishment of the company was architect William Miller and works manager,
Matthew Kemp.
The public company, named the
“Eureka Terra Cotta and Tile Co of Australia Ltd.", was duly formed in May
1914, and took over the existing factory and plant of the proprietary company,
together with the lease of some 100 acres of valuable terra cotta clay deposits
around Ballarat, Creswick and Castlemaine. These creamy, non-adhesive clays
proved to be almost grit free and an enormous asset to the company. The free flowing character of this material
enabled the Eureka factory to mould its Marseilles tiles direct from iron dies;
a far more efficient method than the plaster of paris dies employed by French manufacturers
at the time. Also it appeared that no other area in Australia could offer such
a concentration of suitable clays as Ballarat.